EMS Gas Metering Spanner Set
Precision spanner set for gas meter installations.
EMS Gas Metering Spanner Set
By Sam White
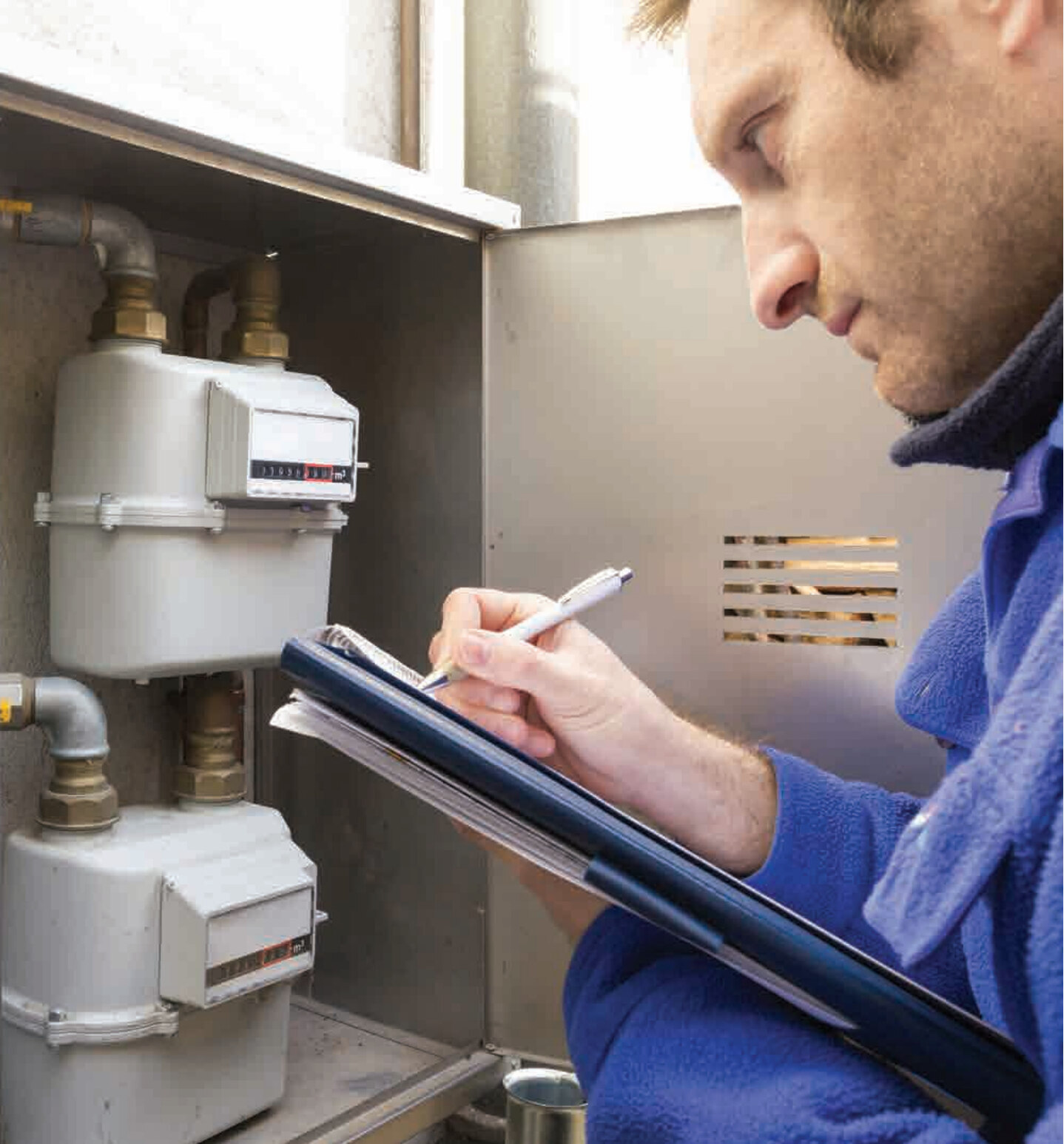
By Sam White, Technical Manager at Energy Metering Solutions and YPPC 2019 finalist
WHEN I FIRST JOINED EMS in
November 2016 and began installing
gas meters, I encountered several
situations that led to a search for more
suitable tooling for the installation and
maintenance of diaphragm gas meters
with threaded connections.
Having identified the issues with
the conventional tooling often used for
these kinds of works, and unsatisfied
with other options available on the
market, I began creating a spanner
set specifically designed to fit the
brass fittings used on domestic and
commercial gas meters, regulators and
flexible connections (spec BS746:2014).
Despite the first version of BS746
being issued in 1937, no other
product has been designed - to my
knowledge - specifically for this
application.
As well as the three sizes of meter
connection, 1in, 1¼in and 2in, there are
also a number of adaptors of different
sizes within the BS746 spec and relating
to BSP pipe thread to BS746.
I identified 14 different sizes across
flat dimensions that would be necessary
to complete the set and allow it to be
used on all available fittings.
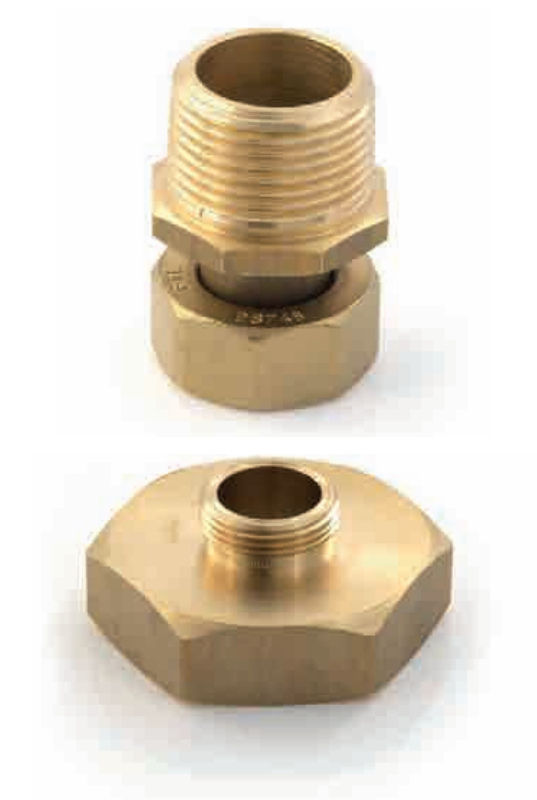
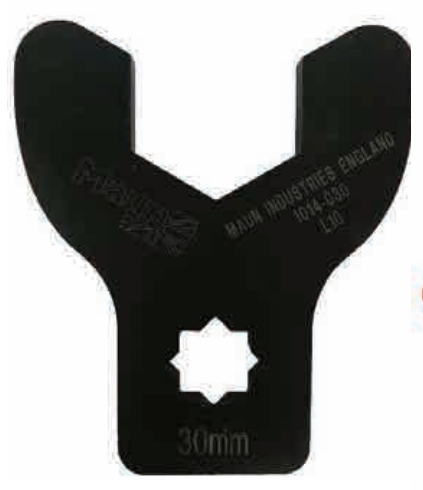
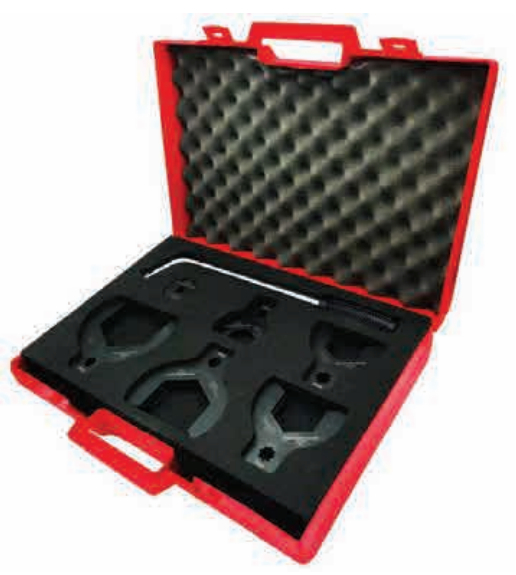
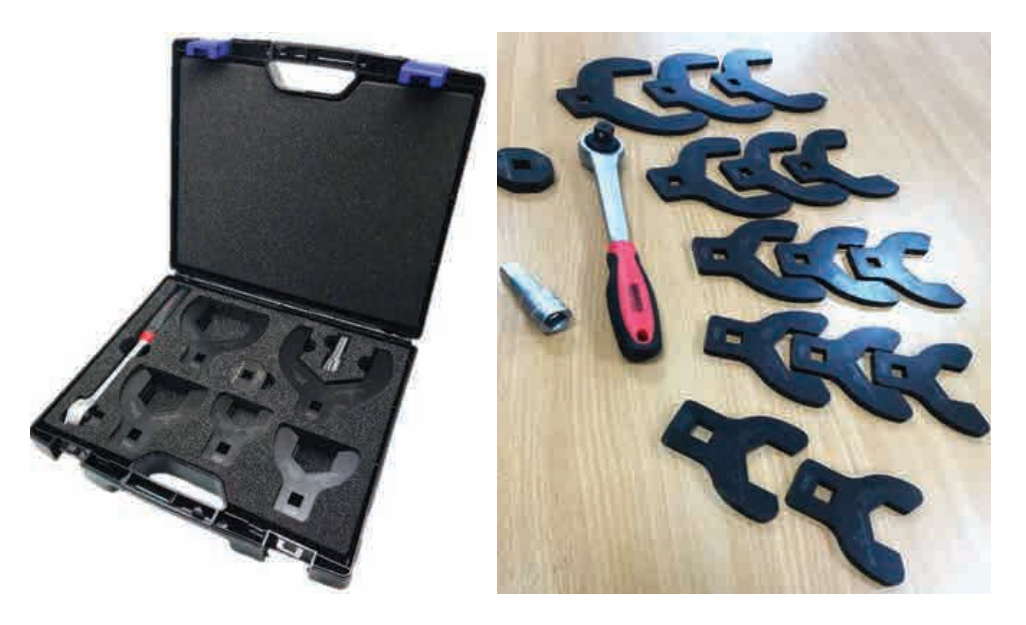
The Problem
The issue I first encountered (and saw repeatedly when exchanging gas meters) was overtightening by the original installer.
Elastomeric washers were brittle and over-compressed on removal. On inspection of the connection on the meter itself, washer seats were often seen to have a layer of thin rust, indicating that moisture had worked into the connection. The likely cause of the corrosion was overtightening of the nut on the meter union, causing excessive compression of the washer.
The washer becomes hardened over time and can no longer accommodate expansion and contraction of the joint with temperature changes, thus leading to leakage and moisture ingress. Most of the time, the leakage is minimal and usually detected by the end user.
However, this situation still causes unnecessary calls to the gas emergency line, load on the network staff to attend and make safe, usually some time off gas for the customer and an attendance by the meter operator to make the repair.
All of this could be avoided by correctly tightening the connection at the time of installation. One of the most extreme cases of overtightening I observed was on an old U40 meter installation in a brick house in a churchyard, which had become excessively corroded. The meter unions were so tight and corroded that when I took a pipe wrench to the fitting, the union was completely seized and the meter connection broke off from the meter casing. The installation had to be cut out and completely re-piped as a result.
Another issue with pipe wrenches and similar tools is they are often toothed, and cause damage to the brass fittings. These can become sharp or rounded off, presenting a cut hazard and the risk of slipping when applying force.
Pipe wrenches in the wrong application have been the cause of many a bruised knuckle, as any pipefitter will confirm. The larger diameters also require a jaw opening up to 86mm, which tends to only be available on large, long tools with handles in excess of 600mm.
These also tend to be weighty, adding to the overtightening problem due to the lever length. To compound all of the above, the meter itself is quite often boxed in or hard to fully access, and once overtightened can make life extremely difficult for engineers in the future.
Initial Design and Manufacture
Once the problems had been identified, I initially had the idea of creating seven double open-ended spanners, with lugs to attach a bar for extra leverage.
I hunted for a manufacturer who would be willing to help me develop the design. Maun Industries was interested and could see the benefit of the innovation to the industry, so we worked on a set of prototypes to be field-tested by EMS and our subcontractors.
The decision was taken in the interest of saving material and weight to separate all the spanner jaws and use a single drive bar. The drive would be via ½in square drive on a breaker bar, with an eight-pointed star cut-out to allow fitting of the drive bar in eight positions.
Also, in the set is an octagonal key for use inside the adaptor fitting, from 2in BSPM to 2in BS746M, which has an internal hexagon profile for fitting. The spanners were to be made of 6mm waterjet cut steel, then case hardened and laser etched.
FIGURE 4 DOMESTIC GAS METER SPANNER SET
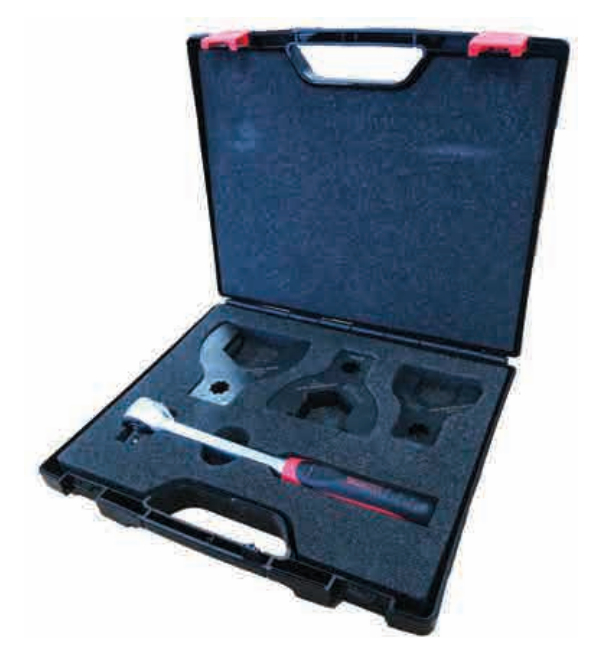
FIGURES OBTAINED FROM BS746:2014 TABLE 1. SPANNER SIZES MATCHED TO WASHER SIZE ON INTENDED FITTINGS
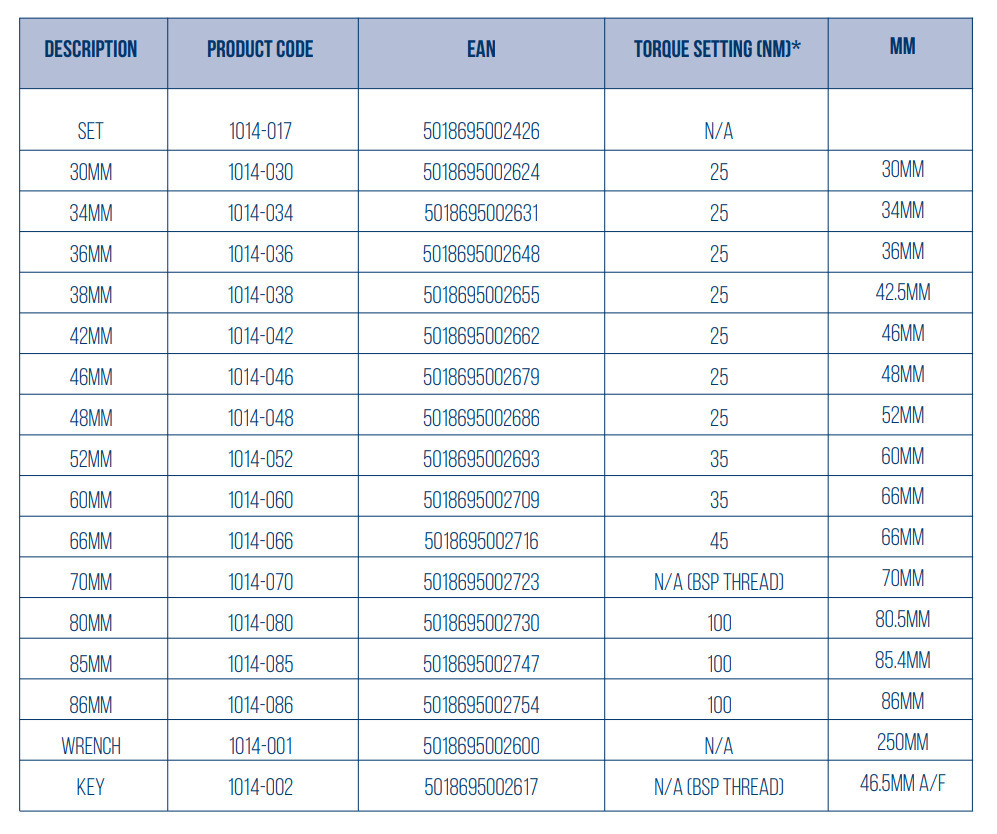
Testing and Development
During field tests it became apparent very
quickly that the angle of the drive bar in
the set made the spanners likely to twist
on application, so I instantly swapped it
for a standard ½in ratchet, bringing the
effort back in line with the nut.
Now there was a ratchet in use, it
became unnecessary to have the eightpointed star, so the next version was to
have a ratchet drive and a square hole
to give a better fit.
Some spanners were a tight fit to
their design, and due to manufacturing
tolerances on the brass nuts, would not
always fit. These sizes were adjusted to
suit and now provide a good fit across
the whole range of unions and adaptors.
Similarly, the key fitting was on the
snug side, so this was adjusted too, and
a short drive extension added to allow
easier access down into the fitting with
the key attached. A smaller box was
sourced and a better layout designed to
keep the spanners secure in the box.
We thought it would be worthwhile to
carry out some destructive testing on the
spanners, which provided results well
in excess of the max strength test figures
stated in BS746:2014, but we did see the
potential for breakage if used incorrectly
Testing results were as follows:
Torque setting (BS746:2014 Table
The decision was taken to upgrade the thickness of the plate to 8mm, providing some extra durability to avoid breakages from overzealous/ inexperienced fitters.
Finished Tool
At the end of the design and testing
process, we were left with a lightweight
tool that could be used in tight spaces,
in excess of 270 degrees rotation
around the fitting thanks to the ratchet,
eliminating slipping and damage to
brass nuts and decreasing the chances
of overtightening with a shorter lever.
With the addition of a short inline
torque adaptor, the force applied can be
read out whilst installing, helping less
experienced engineers to develop a feel
for the correct tightening torque.
There is an option for the set to be
scaled down for domestic meters only
(up to U16), to keep costs and weight
down for the domestic engineer’s
toolset. This is also in final packaging,
mimicking the style of the full set
Conclusion
The thinking behind the development
of this tool is an attempt to change the
way that gas engineers approach their
installations.
There is a widespread belief among
many installers that ‘the tighter, the
better’. That kind of attitude when
working with a metal-rubber-metal seal
can lead to leaks in high frequencies, and
given the softness of brass as a material is
guaranteed to cause damage to the fitting.
With the continued drive for smart
meters, meter exchanges will continue
to increase over the next five years. I
view this as the perfect opportunity to
promote a change in approach and to
ensure that future engineers will be
working on installations that are leak
free, easier and safer to work on. This
should made installers more confident
in their connections to meters on
completion of the job.
With this tool, I believe we’ve taken
a step towards how things should
be done, rather than accepting the
way things are, and hopefully we can
continue to look for new innovations to
make gas safer for everyone.
References
BS746:2014 – Specification for gas meter unions and adaptors
Acknowledgements
Thanks to the following people and organisations whose support made the development possible: Deep Valecha, Operations Director, Regent Gas, for sponsoring the development and patent filing for the invention; Phil Casper, Managing Director of PJ Casper Associates and consultant to EMS, for mentorship throughout the project; Maun Industries for their expertise and commitment to the development, design and manufacture; EMS subcontractors for field testing and feedback.